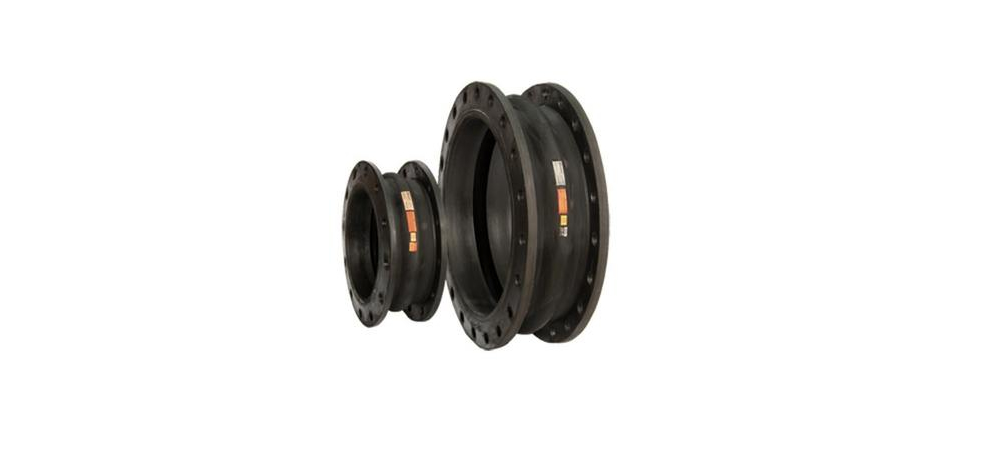
Full Face Rubber Flexible Connectors
Product Code: FF
EMFLEX full faced rubber flexible connectors are comprised of a synthetic rubber membrane reinforced with synthetic fibre. The membrane finishes with a full face behind which are carbon steel split backing flanges. The rubber face is drilled to match the flange table. They are capable of absorbing movement in several directions; axial compression, axial elongation and lateral deflection. A small amount of angular movement may also be allowed. They are designed to allow for movements in pipework systems due to thermal changes. This relieves stresses, protects machinery attached to the pipework, and thus lengthens the life of the whole system. Their ability to flex axially and laterally also allows for isolation of vibration, reduction in noise transmission and compensation for pipework misalignment. These flexible connectors are custom built to suit the requirements of pressure and temperature.
Product Type
Additional Information
A full faced rubber membrane with untied flanges.
A full faced rubber membrane with tied flanges.
Working Pressure
These units are custom built to suit working pressure requirements.
Test Pressure
Generally a test pressure of 1.5 x required working pressure is allowed for, however units will be designed to system requirements.
Working Temperature
This is dependent on rubber type and synthetic fibre type used.
Vacuum Conditions
Vacuum support rings are available for vacuum conditions to prevent distortion of the unit.
Design Consideration
Rubber flexible connectors are subject to the same internal pressure force as metal expansion joints and the force is equal to the internal pressure multiplied by the maximum internal area. This force causes the connector to lengthen and tied units are recommended where the working pressure exceeds 4 bar, unless the pipework is secured to restrict movement.
When using with plant items mounted on vibration isolators, such as springs or inertia bases, then TIED UNITS must be installed.
Material Specifications
These units can be manufactured from many different rubber compounds to suit a wide variety of media. The following is a list of the more frequently used compounds with an indication of capabilities:-
Neoprene – has excellent weathering resistance and good ageing and abrasion qualities, as well as good oil resistance.
Chlorobutyl – has high temperature resistance and excellent weathering resistance. Nitrile – has excellent resistance to oil, grease and fuels, as well as good heat resistance.
Hypalon – has excellent ozone and weathering resistance, and is used mainly with oxidising acids.
Viton – has excellent high temperature and chemical resistance. Backing flanges are carbon steel and reinforcement is nylon for standard units; other materials can be used on request.
Additional Equipment
Fairing Pieces – are an internal sleeve, normally manufactured from the same compound as the lining of the unit. Metallic fairing pieces can also be supplied.
External Support Rings – are needed where high temperatures and / or pressures occur.
Fireguards – completely enclose the unit to protect it from flames in the event of a fire. Since it is more flexible than the unit, the performance is not impaired.
+ -
Emflex
FULL FACED RUBBER HANDBUILT
N.Minikin & Sons LimitedUnit 2B Brickyard Road, Roecliffe, York, YO51 9NS
Email: enquiries@minikins.co.uk Web: www.minikins.co.uk
Tel: 01423 326 789
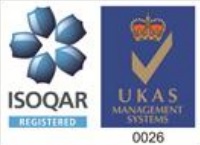
01423 326 789
N.MINIKINS & SONS LIMITED
MINIKINS.CO.UK
Full Face Rubber Flexible ConnectorsProduct Code: FF
EMFLEX full faced rubber flexible connectors are comprised of a synthetic rubber membrane reinforced with synthetic fibre. The membrane finishes with a full face behind which are carbon steel split backing flanges. The rubber face is drilled to match the flange table. They are capable of absorbing movement in several directions; axial compression, axial elongation and lateral deflection. A small amount of angular movement may also be allowed. They are designed to allow for movements in pipework systems due to thermal changes. This relieves stresses, protects machinery attached to the pipework, and thus lengthens the life of the whole system. Their ability to flex axially and laterally also allows for isolation of vibration, reduction in noise transmission and compensation for pipework misalignment. These flexible connectors are custom built to suit the requirements of pressure and temperature.
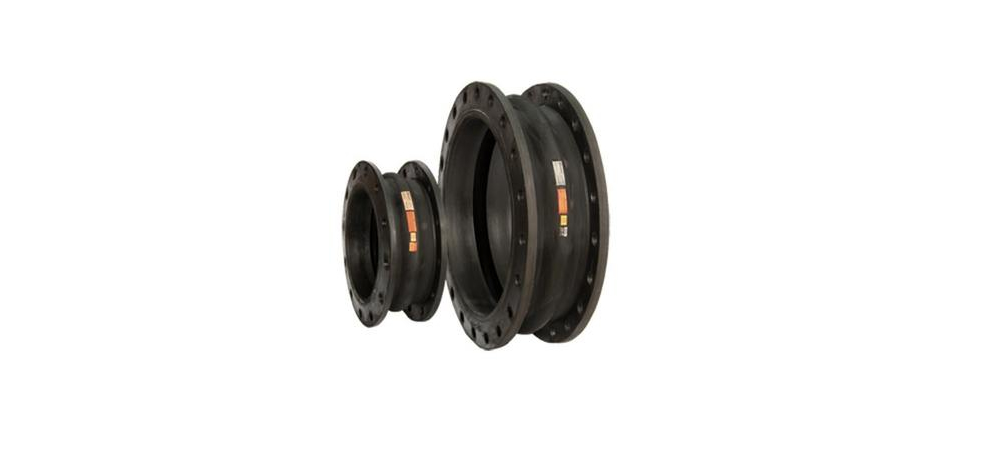
A full faced rubber membrane with untied flanges.
A full faced rubber membrane with tied flanges.
Working Pressure
These units are custom built to suit working pressure requirements.
Test Pressure
Generally a test pressure of 1.5 x required working pressure is allowed for, however units will be designed to system requirements.
Working Temperature
This is dependent on rubber type and synthetic fibre type used.
Vacuum Conditions
Vacuum support rings are available for vacuum conditions to prevent distortion of the unit.
Design Consideration
Rubber flexible connectors are subject to the same internal pressure force as metal expansion joints and the force is equal to the internal pressure multiplied by the maximum internal area. This force causes the connector to lengthen and tied units are recommended where the working pressure exceeds 4 bar, unless the pipework is secured to restrict movement.
When using with plant items mounted on vibration isolators, such as springs or inertia bases, then TIED UNITS must be installed.
Material Specifications
These units can be manufactured from many different rubber compounds to suit a wide variety of media. The following is a list of the more frequently used compounds with an indication of capabilities:-
Neoprene – has excellent weathering resistance and good ageing and abrasion qualities, as well as good oil resistance.
Chlorobutyl – has high temperature resistance and excellent weathering resistance. Nitrile – has excellent resistance to oil, grease and fuels, as well as good heat resistance.
Hypalon – has excellent ozone and weathering resistance, and is used mainly with oxidising acids.
Viton – has excellent high temperature and chemical resistance. Backing flanges are carbon steel and reinforcement is nylon for standard units; other materials can be used on request.
Additional Equipment
Fairing Pieces – are an internal sleeve, normally manufactured from the same compound as the lining of the unit. Metallic fairing pieces can also be supplied.
External Support Rings – are needed where high temperatures and / or pressures occur.
Fireguards – completely enclose the unit to protect it from flames in the event of a fire. Since it is more flexible than the unit, the performance is not impaired.
01423 326 789
N.MINIKINS & SONS LIMITED
MINIKINS.CO.UK